Scheduling and Demand Balancing
Scheduling Staff and Demand Balancing. Understand the relationship between your demand and the staff you need to meet that demand.
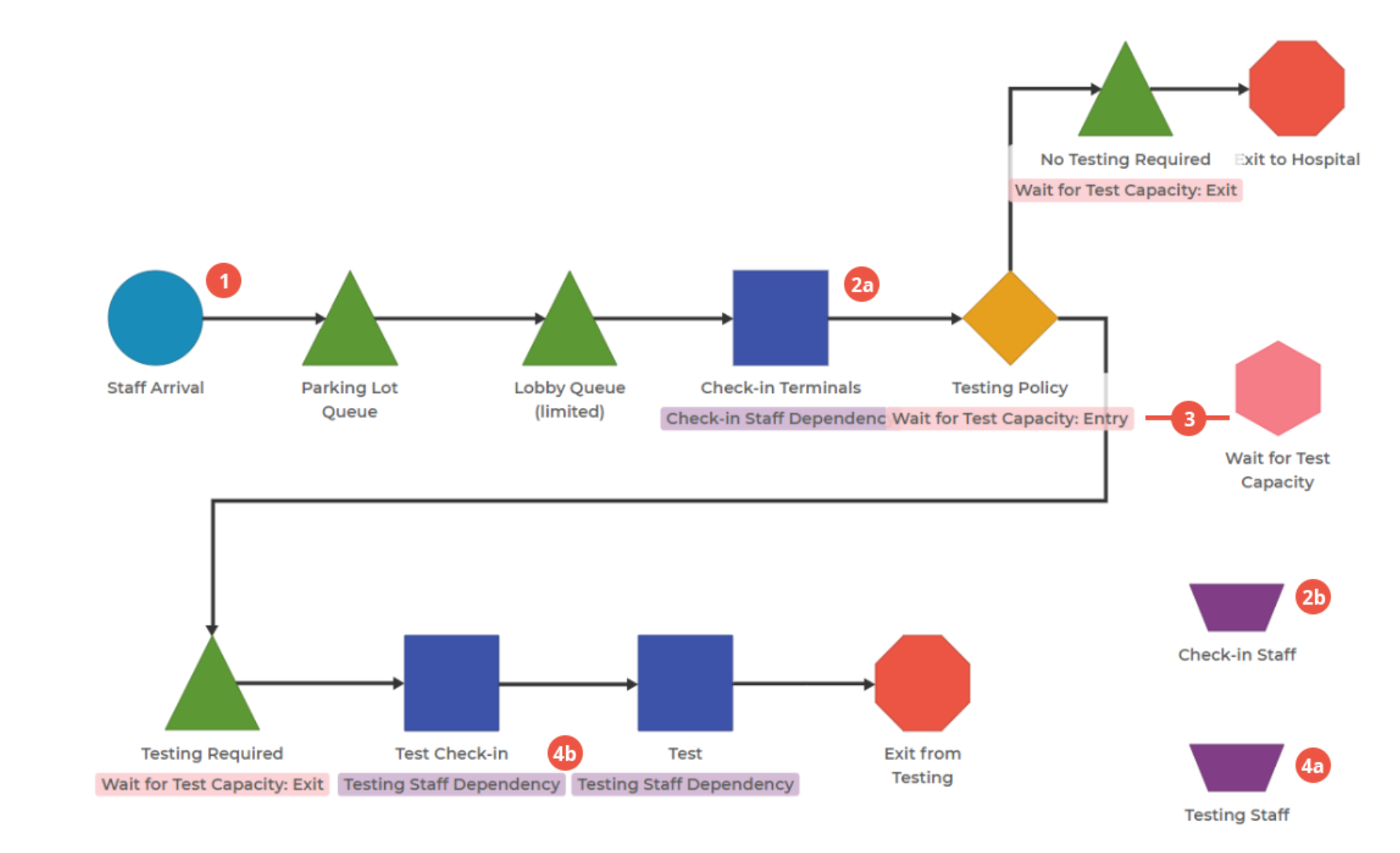
1. Schedule Demand. Start and stop demand based on simulation time. In this model, we layer the same “Hospital Staff” item to achieve different numbers of people arriving at different times. You could also use this method to start and stop demand for different items at different times, such as on a production line.
2. Staff the Check-In Terminals. The Activity Block (2a) has 8 Check-in Terminal machines, but all 8 don’t have to be staffed simultaneously. The Resource Block (2b) allows you to set a staff schedule and indicate how many Terminals (machine + staff) should be running at particular times in the model.
3. Block people from moving if the “Testing Required” room is full. This Core Process Pull block limits the number of people in the three marked blocks to 8 people. Since most people will pass through the ‘No Testing Required’ block to Exit, this model will only really be affected if ‘Testing Required’ increases to 8 people. If so, no person will move into the ‘Testing Policy’ decision block until someone leaves the ‘Testing Required’ block. This, in turn, will back up the ‘Check-in Terminals’ and so on.
4. Applying the Same Pool of Resources to Multiple Activities. The Testing Staff (4a) is split between two different activities (4b). Each staff member can only work on one activity at a time, but can be split up between the blocks they are assigned to, allowing both Activities to run at the same time. When you have a schedule that includes times when only one ‘Testing Staff’ is available, that staff member moves between the two activities. One activity will be inactive when the staff member is working the other activity.
Bonus! This model is based on a true story.
A hospital was struggling with hours-long waits to get through check-in and testing. The initial solution was to duplicate this process, which would add capacity, but would also increase the cost by thousands of dollars a week.
By using Lean principles to balance the demand by adjusting work start times and using a model like this to experiment with the scheduling, the team avoided the additional expenses, saved hours lost waiting in lines, and eliminated issues with physical distancing.
Was this helpful?