Process Modeling Fuels Operational Excellence in High-Stakes Industry
In the best of circumstances, it's no easy task to implement process improvements on the manufacturing floor in any industry – but it's a particularly thorny prospect when people's lives depend on the quality of the medical devices being created by the process.
This has long been the high-stakes dilemma for continuous improvement initiatives at Medtronic PLC, one of the world's preeminent medical device manufacturers. For over 60 years, Medtronic has been a global leader in healthcare technology, producing groundbreaking medical devices like cardiac pacemakers and stents, surgical robotics, insulin pumps, and other surgical tools for 70 different health conditions. A strong emphasis on operational excellence is imperative because of the direct impact on human lives. The company's decades-long continuous improvement journey has realized major gains in product quality, labor efficiency, and lead time.
These wins come in a space where the "test and learn" ethos of process excellence clashes with notoriously stringent regulations on medical devices. Federal guidelines for the industry extend beyond the products themselves to include all elements of the production process and any changes to it. Incremental learning cycles and improvement by trial and error are not welcome because there is no room for error.
"We can't just go change something on a production line and hope that it's good," said Ryan Magnuson, the Senior Operational Excellence Program Manager at Medtronic.
"We have to go through really strict validation requirements to be able to prove to our regulatory authorities that we understand the impacts of any process changes because everything we do impacts human health."
In short, Medtronic needs iron-clad evidence that process changes will work before those changes are approved and implemented.
Data-Driven Design: Testing Before Investing
All of these complexities and constraints were in full force when a Medtronic Green Belt was analyzing data from a medical device manufacturing site in Colorado that produces vessel-seal dissectors. These tools, used to seal blood vessels in laparoscopic surgeries, have seen steady increases in demand over time – challenging production capacities and placing a premium on raising output without sacrificing quality. The Green Belt project was chartered to help improve operating efficiencies and meet demand.
The problem? Data from value stream maps of the production line weren't offering the Medtronic team the needed visibility into the variation holding the line back. Staple Lean metrics like average cycle time and takt time failed to reveal any significant discoveries. Variation, the real source of production bottlenecks, was lurking.
An average is useless information when looking at process performance over time. Problems don’t happen because of averages; they happen because of variation.
To get beyond averaged data that were masking true sources of variation, Medtronic turned to MoreSteam's Process Playground software, a web-based tool for creating virtual process models, or "digital twins" of processes. By constructing data-driven models of the real world, teams can better understand the current state. That baseline model is created in the Define phase of a DMAIC project to validate knowledge of the process. Then, as teams identify potential improvements in the Analyze and Improve phases of the project, they can test their hypotheses using the model to verify changes and stress-test the new process design.
Magnuson believes the crucial benefit of Process Playground is in the level of detail it affords in mapping out current and future states. Medtronic leaders can now simulate much more than average effects - they can now model variation within process steps, cycle-to-cycle, and shift-to-shift. Magnuson said this allowed for an accurate picture of how that variation, over time, was holding the line back from fully utilizing labor capacity on the Green Belt project in question.
Accelerating Improvement
Using Process Playground, the Medtronic team was able to quickly and safely test an obvious but expensive possibility to increase capacity: duplicating the line. By examining the data on units per labor hour and other cycle-to-cycle metrics, leaders determined that while such a change would produce more incremental units, the underlying inefficiencies would be unresolved.
With that radical change ruled out, leaders zeroed in on a much more effective - and much less costly and disruptive - change: tackling the most wasteful sources of variation, increasing process stability over time, and generating the needed output efficiency gains. By identifying and resolving sources of variation, a revised process design was tested with a virtual process model, then approved and implemented, yielding an 11.6% output improvement without any additional capital expenditure. Medtronic got the results of a duplicated production line at a fraction of the cost, and what would have been a months-long process took only a matter of weeks - a very successful Green Belt project!
Process Playground is a really powerful tool.
On another project, after building multiple process models to test new ideas, an optimized future state was designed and implemented, resulting in nearly doubled output and an increase in operator and machine utilization from ~70% to 98%.
A New Paradigm
The traditional approach to Lean improvement is built on tried and true methods predicated on cycles of small experiments, learning, and change. Many argue that it's a dependable approach that works really well, but we can be better at small experiments and speed up the learning cycles. If we can do them virtually, at least to a large extent, the process design can be fine-tuned before implementation. And we can move from an ad-hoc observation-based approach to more of a data-driven method that marries analytics and lean thinking into a new paradigm of process design.
Medtronic has made process modeling a standard element of its lean transformation playbook, inserting virtual prototype process stress-testing as pre-work for the 3-P step with its cardboard mock-ups and production preparation.
Building a rapid virtual prototype provides multiple benefits, quickly and inexpensively:
- The exploration of a much wider design space than would typically be considered, with "crazy" what-if scenarios evaluated with a few mouse clicks
- Validation of performance metrics and fine-tuning of input parameters
- Stress-testing under different scenarios to identify likely points of failure
- Evidence to support investment/financial decisions
- A visual model for training operators
Magnuson summarizes his experiences:
Process modeling allows us to be incredibly efficient and a lot more creative in our hypothesis testing because we can dream big, right? It's just a matter of changing parameters in the model, and we can show each other and show our users and operators: 'Well, if we make this change, this is what will happen to our output' - and it's just a matter of clicks. And if it doesn't work, we didn't waste anybody's time; we didn't waste any material or anything like that, and we can move on to the next option. So, it helps us with our hypothesis testing and creative problem-solving and makes us more confident in the output of those studies. We're not just looking at individual data points. We have a model that we trust that shows, hey, if we make these changes, we can be really confident in the output.
Getting Started
Process Playground is just one component of Medtronic’s MoreSteam-enabled arsenal of process improvement tools. The company uses MoreSteam for all its Yellow Belt, Green Belt, and Master Black Belt training, with Green Belts and above trained on Process Playground.
“Not that the tool requires even that much training,” Magnuson said. “With most modeling software, the barrier to entry is so high, and the technology is so complex, you can see people’s eyes glazing over,” he said. “Process Playground is so elegantly simple. Give people a couple of intros, and they’re off and running.”
“It's really transformed our Lean thinking…that we need to understand variation as a key contributor to most problems and as a source of waste that we need to drive out of our processes.”
Last Words
MoreSteam CEO William Hathaway believes that Medtronic has forged a global best practice:
Medtronic's approach to process improvement truly presents a new paradigm of lean process design, using quick and inexpensive virtual prototyping to learn quickly and effect changes with greater certainty of success. I see this as a real synthesis of lean and Six Sigma - to use data-driven analytics and lean thinking to drive process design changes without all the trial and error that nobody really has time for. It's world-class.
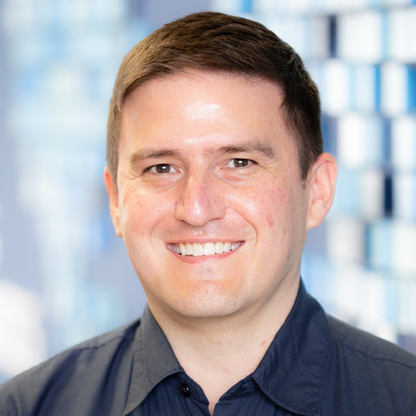
Director of Global Operational Excellence • Medtronic
Ryan Magnuson has been with Medtronic for over eight years and is currently the Senior Operational Excellence Program Manager. Ryan is a certified Master Black Belt by MoreSteam and The Ohio State University and is part of the Enterprise Process and Leadership Excellence team. He has a Bachelor of Science in Pharmacology and a Bachelor of Arts in Philosophy from the University of California, Santa Barbara. Ryan is skilled in project management, statistics, business intelligence tools and analytics, DMAIC A3 methodology, Lean Six Sigma, and Failure Mode and Effects Analysis (FMEA).