A Beginner’s Guide: What is Design for Six Sigma?
February 9, 2024It's no secret that redesigning an existing product to better meet customer needs is expensive and wasteful. The time and effort it takes to test and develop multiple iterations of the same product before reintroducing it to the market is valuable time that you could have spent elsewhere had the product met the customer's expectations and had a higher level of quality from the start.
Design for Six Sigma's objective is to do additional work today to ensure there won't be rework tomorrow. Fully aligning a design with your customer’s needs and expectations before the design's completion significantly decreases the chances of correcting defects or issues after implementation.
With nearly every industry growing increasingly competitive, getting your products and processes right the first time is more crucial than ever.
What is Design for Six Sigma?
Unlike traditional Lean Six Sigma, which primarily focuses on process improvement, Design for Six Sigma is a methodology and set of best practices focusing on developing new products and processes that are robust, reliable, and capable of consistently delivering high-quality results. DFSS places a strong emphasis on understanding and meeting customer requirements from the outset of a project rather than trying to correct defects or issues after implementation.
Why is Design for Six Sigma Important?
Let’s revisit an anecdotal example of the importance of good design, told by MoreSteam’s founder and CEO, Bill Hathaway:
DFSS is sometimes regarded as too complicated and more complex than DMAIC. I think the converse is generally true. DFSS principles are often more intuitive than DMAIC.
I recently went to a mass-market optical store to buy a pair of reading glasses. As you may know, reading glasses come at various standard "power" levels, such as +1.0 or +2.5, with the strength of magnification increasing along with the number. Looking at the rack of glasses, I was confronted by the situation depicted below: The power rating was printed in small white text with poor resolution against a light green background. When I held the glasses far enough away to try and read the text, the text was too small and faint to read. I was amused that I was unable to buy reading glasses unless I already had reading glasses.
Let's assume for a moment that the reason someone buys glasses is because they CAN'T READ. Armed with this insightful VOC, I might propose a simple modification to the label system that I experienced – something more like this:
Sometimes, good design is just a matter of attention to customers' requirements and some common sense.
This story is a great, real-life example of why good design matters from the start. When the customer lacks visibility into the quality or functions of the product they are looking to purchase, the chances of them making said purchase could significantly decrease. Customers want both transparency and the feeling that you are meeting their needs. And especially in today's digital era, where reviews, communications, and discussions can unfold instantaneously, redesigning a flawed product could prove more damaging to an organization's reputation than getting it right the first time.
There are myriad reasons why DFSS is essential that may go with or without saying – proactive quality assurance, time and cost savings, risk reduction, consistency, and predictability; the list goes on and on. But it is particularly essential in industries where innovation, quality, and customer satisfaction are critical.
How is DFSS Different from Traditional Lean Six Sigma?
Design for Six Sigma and Lean Six Sigma are different methodologies that serve different purposes. However, they do share many similarities:
- A strong focus on the customer. Lean Six Sigma and DFSS prioritize customer satisfaction by identifying and meeting customer needs and expectations.
- Driving a culture of process improvement. Both practices aim to improve processes and deliver high-quality products or services. They also often involve cross-functional teams and collaboration across departments to analyze and improve processes or ensure comprehensive consideration of design elements.
- A data-driven approach. Lean Six Sigma emphasizes using statistical tools and data analysis to understand and improve processes, while DFSS utilizes statistical methods and analysis throughout the design process to ensure reliable outcomes.
- The use of roadmaps. Problem-solving roadmaps are standard tools for both methodologies. And while the roadmap chosen should depend on your problem's scope, Lean Six Sigma projects often involve the DMAIC method, and DFSS projects involve IDOV.
- An emphasis on risk management. Both Lean Six Sigma and DFSS often incorporate tools like Failure Mode and Effects Analysis (FMEA) to identify and mitigate potential risks.
Both methodologies complement each other within a comprehensive quality management framework. But these two methods are not the same, and it’s also worth noting how they differ. Aside from each of their primary focuses and goals, other differences include:
- The timing of implementation. Lean Six Sigma is typically applied to an existing process that needs improvement or optimization, while DFSS is implemented during the design phase before the launch of a product or process.
- The tools and techniques used. There is undoubtedly a Venn diagram when it comes to the tools that Lean Six Sigma and DFSS use. But, since Design for Six Sigma operates almost exclusively in the design phase, the tools associated with the method will reflect just that; techniques like SPC, process mapping, and the 5 Whys are common amongst DFSS practices.
- The focal point of the project life cycle. Lean Six Sigma typically involves projects with a well-established process that needs improvement. DFSS projects focus on the entire life cycle of designing and implementing new products or processes. The duration of each type of project varies based on several factors, like the complexity of the problem or goal, the scope of the project, the industry, the resources allocated, and the organization's commitment to the process improvement initiative.
What Does a DFSS Certification Entail?
The specific details of DFSS certification programs can vary depending on the certifying body or organization offering the credential. But some standard components that you can typically expect include:
- Proof of prerequisite knowledge, such as a basic understanding of Lean Six Sigma principles or completion of foundational Lean Six Sigma training, like Green or Black Belt.
- Training courses that cover key concepts, methodologies, and tools associated with DFSS, like the IDOV framework, FMEA, robust design principles, and statistical methods in design.
- Practical application through hands-on projects, either actual or simulated, that help reinforce the knowledge you gain in the training.
- Exams or assessments that evaluate your understanding and comprehension of the material.
- Varying levels of certification that represent different degrees of proficiency and responsibility, similar to Yellow Belt, Green Belt, and Black Belt.
In MoreSteam's case, our design programs mirror our Green and Black Belt training that follows the DMAIC method. It includes complete and robust training with built-in simulations to practice and gain experience, a final exam, and either one or two project requirements, depending on the certification level you seek.
Our design programs differ from what you would typically see because the curriculum offers a broader scope than Design for Six Sigma. It heavily emphasizes experimentation and iterative design through physical and virtual prototyping. Learners experiment with and stress-test 'virtual twins' of their processes through our discrete event simulation software, Process Playground. Process Playground offers a low-cost, low-stakes environment that is, nonetheless, high-fidelity. Our Design for Green Belt and Design for Black Belt courses also prioritize thoughtfully designing processes and products that anticipate, meet, and exceed customer needs – a goal that extends well beyond achieving a specific Sigma Level.
Customer needs that are not met from the outset can lead to decreased visibility, costly rework, and, ultimately, dissatisfaction. In this fast-paced world where it's easy to fall behind your competitors, and customer expectations are ever-growing, adopting DFSS into your organization represents a commitment to excellence, customer satisfaction, and sustainable success.
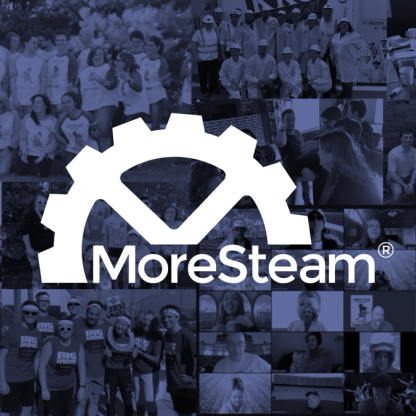
MoreSteam's Enterprise Process Improvement platform includes the tools, training, and software you need to transform your organization, large or small, into a problem-solving powerhouse. Our products are trusted by over half of the Fortune 500 and by other organizations and universities worldwide. When you partner with MoreSteam you gain a team dedicated to helping you succeed.