Resources for Operational Excellence
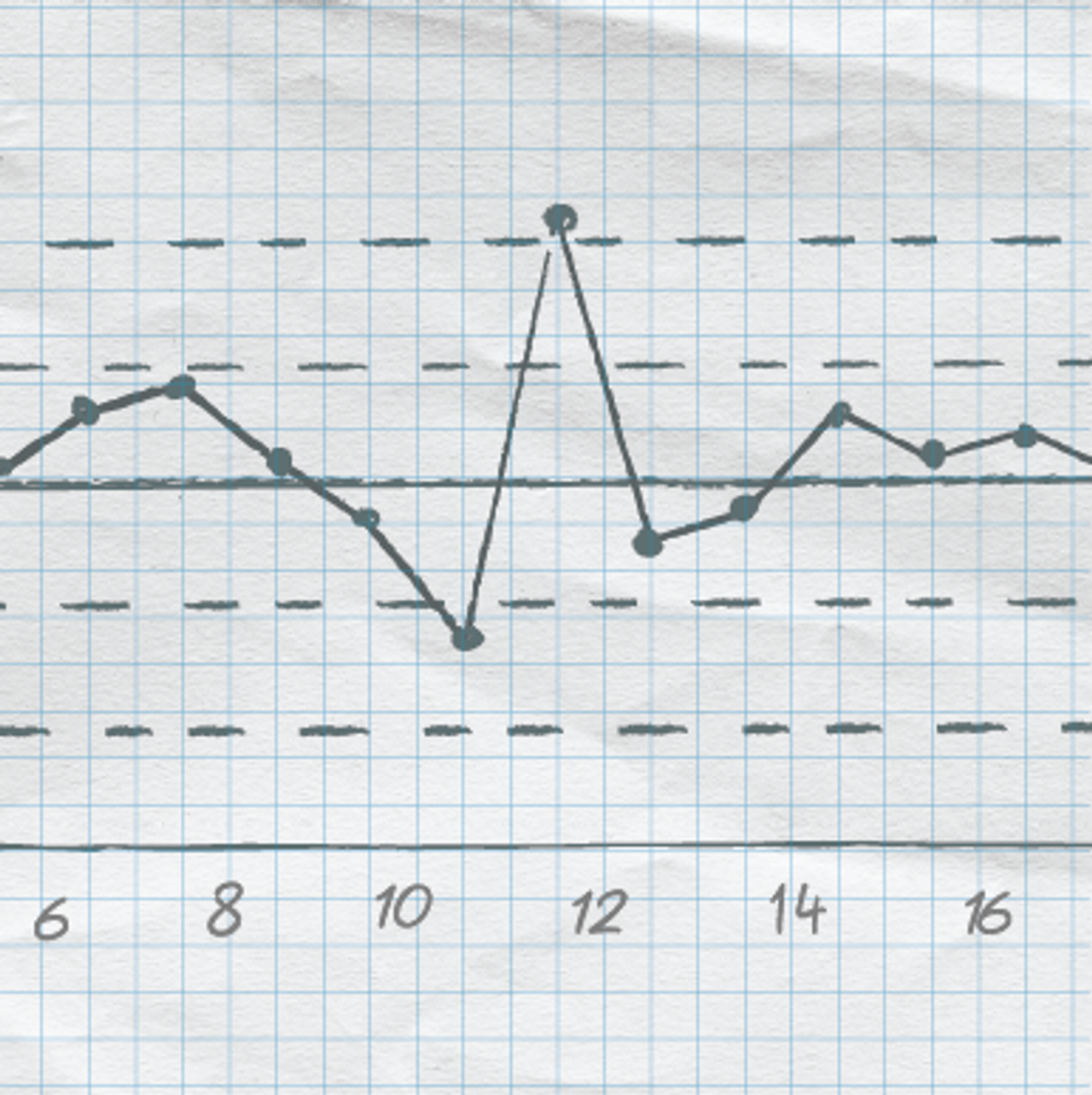
A Review of "A Better DMAIC"
Read More
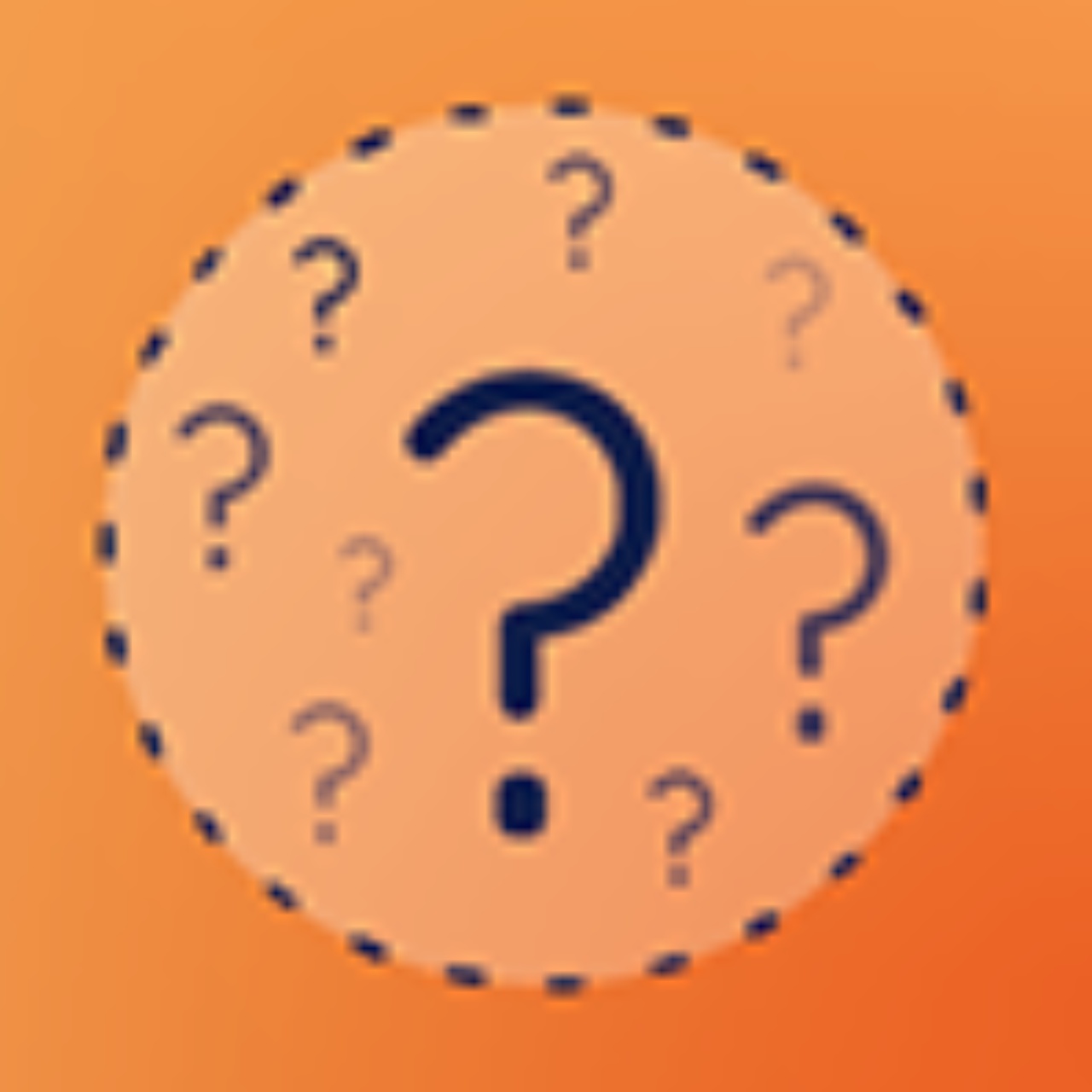
Why the Most Critical Phase is Often the Most Overlooked
Read More
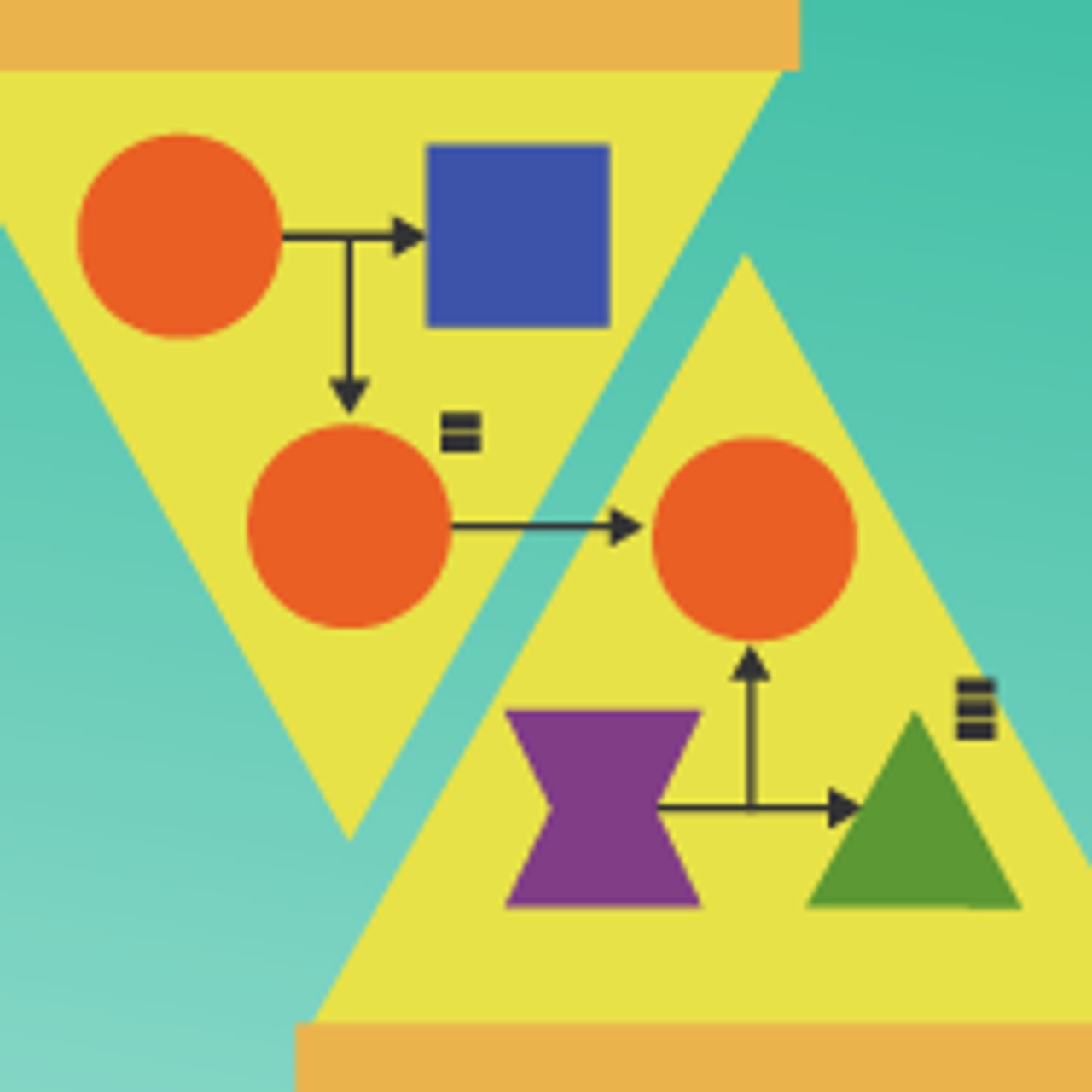
Using Modeling to Teach Lean Six Sigma & DMAIC
Read More
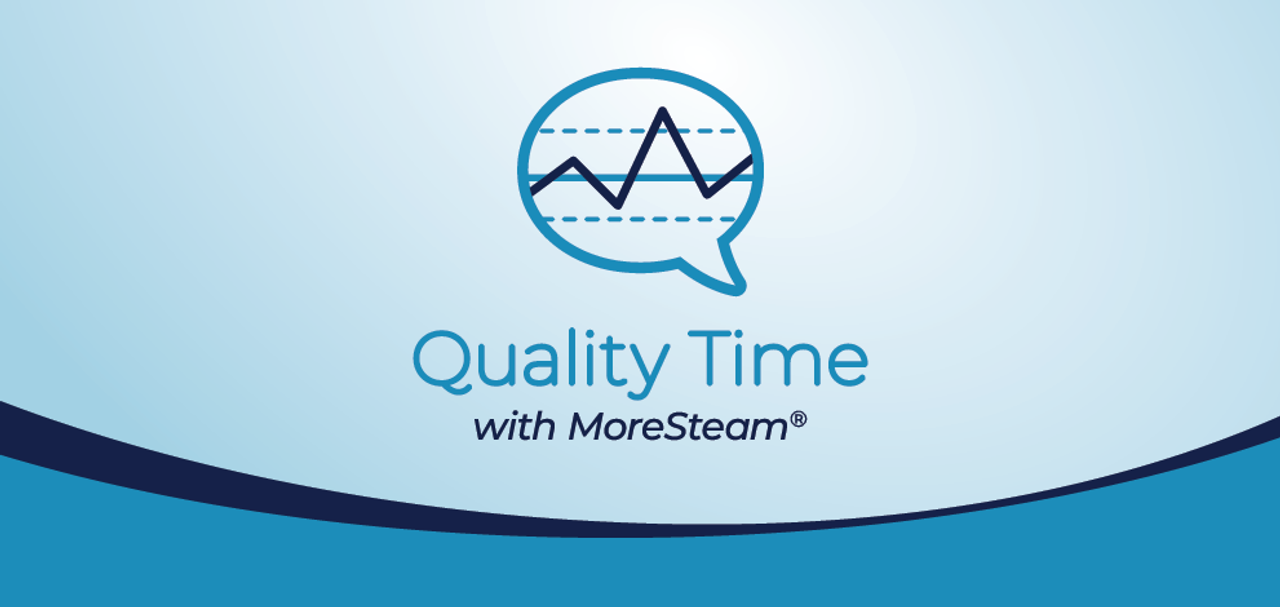
Quality Time Podcast: Leadership, Coaching, and Lean Tailgating with Ken Robinette
Read More
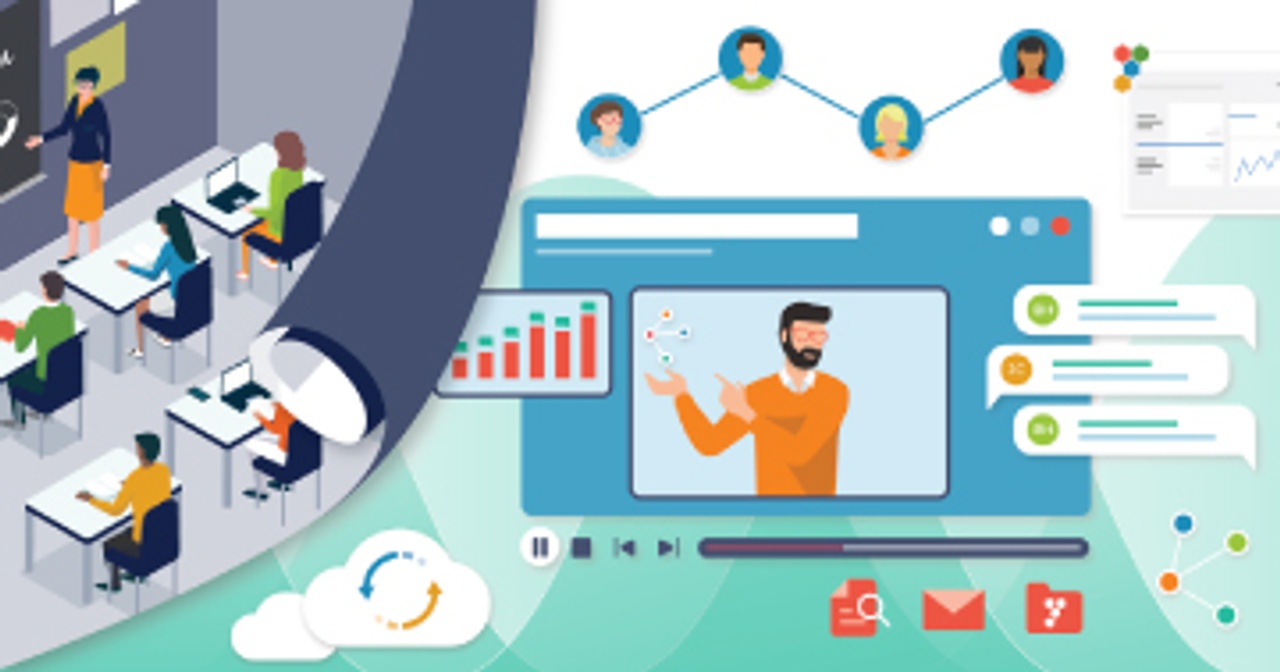
Blended Learning Keeps Classroom Productive
Read More
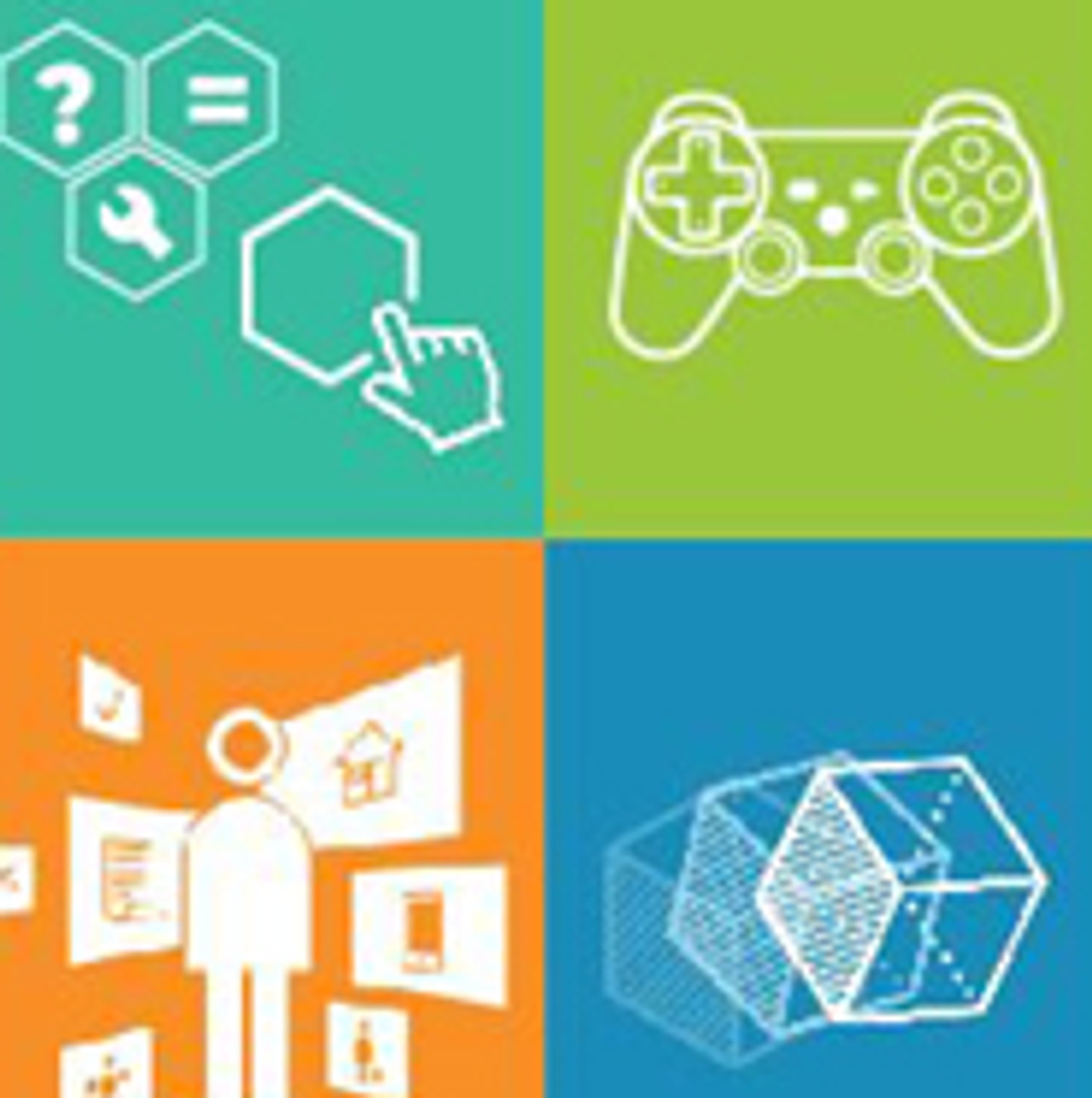
Better Methods to Learn Better Methods
Read More
Project Management
- How TRACtion Solves 5 Common Project Management Challenges
- Aurorium’s TRACtion Success – From Spreadsheets to a Single Source of Truth
- The Perfect Pair: Lean Six Sigma Project Management with Traction & EngineRoom
- 900 Project Charters and Counting
- Best Practices of Lean Six Sigma Project Management and Tracking Tools
- Maximize Project Impact with the Right Lean Six Sigma Project Tracking Tool
New to Lean Six Sigma
- A Beginner's Guide: What is Lean Six Sigma?
- Lean Six Sigma Belt Levels Explained
- What is the DMAIC Methodology?
- Why the Most Critical Phase is Often the Most Overlooked
- Applying Lean to Six Sigma Training
- Rapper Highlights the Fun Side of Lean Six Sigma
- Selecting the Right Green Belt Training and Certification Program for You
Data Analysis & Statistics
- Mastering Destructive Gauge R&R
- The Top 5 EngineRoom Features That Make Data Analysis Easy
- Power of a Statistical Test
- The Beginner's Guide to Discrete Event Simulation
- Classification and Regression Trees Explained
- Unlocking the Power of Statistical Hypothesis Testing: A Fresh Approach
- If You Learn One Statistical Tool for Process Improvement, Make It Control Charts
Leadership & Culture
OpEx Field Notes
Upcoming Events
Lean Six Sigma Resources for Continuous Improvement and Operational Excellence
Welcome to MoreSteam's Lean Six Sigma Resource Library—a curated hub of content for professionals focused on process improvement, operational excellence, and continuous learning. Whether you're starting your Lean Six Sigma journey or advancing an enterprise-wide initiative, this page offers a diverse collection of tools and insights to help you solve problems and drive measurable impact.
Explore expert-led webinars, in-depth case studies, white papers, blogs, and podcasts—all designed to help you apply Lean Six Sigma principles in real-world settings. Learn how organizations across industries are using tools like value stream mapping and root cause analysis to reduce waste and improve quality. From foundational concepts to emerging trends in AI and digital transformation, these Lean Six Sigma resources support your growth as a problem-solver and leader in operational excellence. Whether you're looking for inspiration, training, or tactical guidance, the MoreSteam Resource Library is your go-to destination.
Many of these Lean Six Sigma resources also feature tools developed by MoreSteam, such as EngineRoom for data analysis and TRACtion for project tracking. Whether you're validating a process map or leading a team through DMAIC, these OpEx resources provide practical support for continuous improvement.
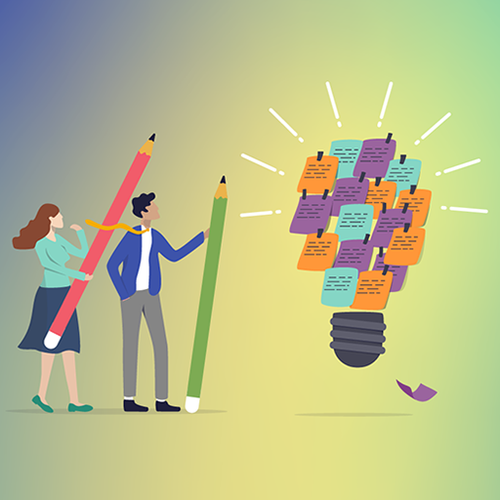