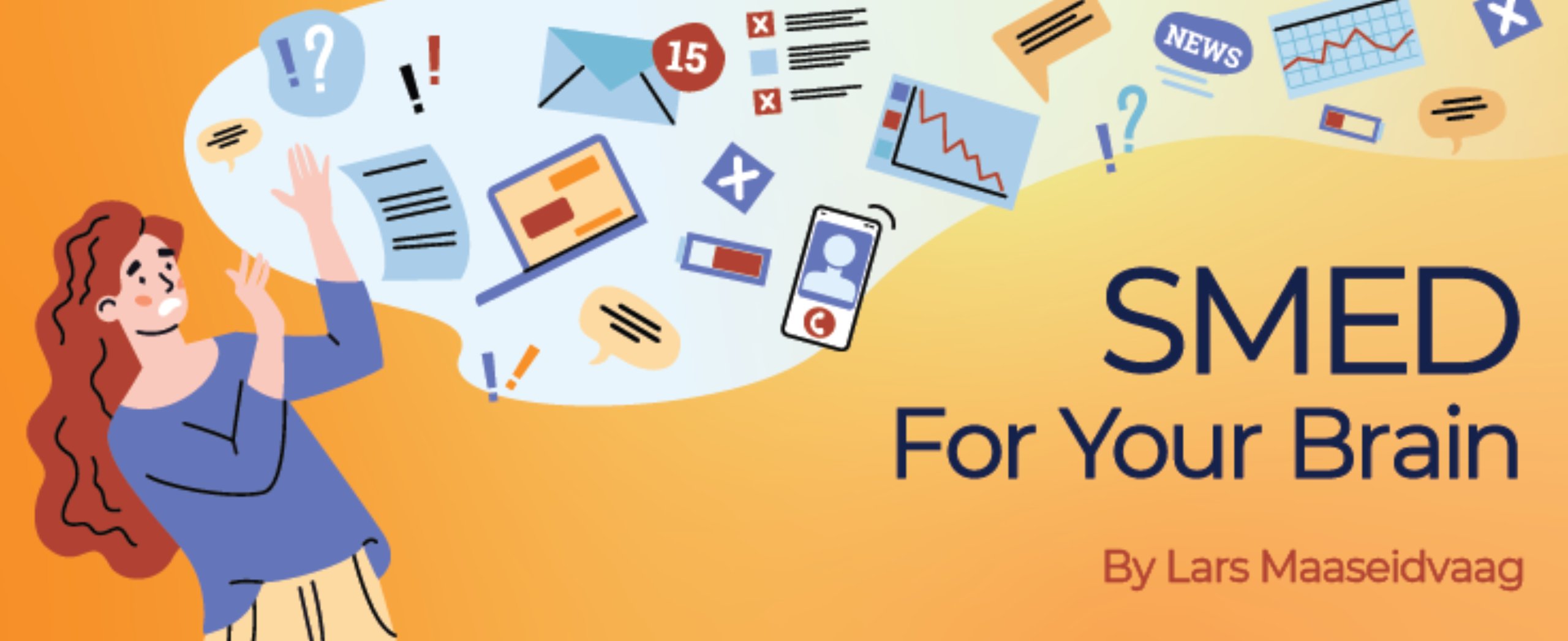
What Would You Do for 15 More Points of IQ?
August 12, 2022The irony is inescapable as I finally sit down to write this blog, a month late and with a countdown ticking. I've been trying to write a blog on multitasking. But I haven't gotten to it...because of too much multitasking.
The motivation for this blog started with my previous blog on the great resignation and the resulting tight labor market. Fewer workers with fewer resources are trying to satisfy the increasing demand for products and services. That's a tricky equation to balance.
With fewer employees and resources in the workplace, current hires are forced to multitask, something our brains are not wired to do. But what is the benefit of several mediocre results instead of one outstanding result?
Until the labor and resource shortage changes, we'll need to figure out how to multitask efficiently. Is it possible to approach this situation through lean thinking?
Although typically used in manufacturing, the rapid changeover methodology, or SMED (Single Minute Exchange of Dies), may be useful in combating our multitasking behaviors.
An inevitable outcome of trying to balance that equation is multitasking. Everything still needs to get done, and in most cases, a sequence of operations or activities still needs to happen, so we begin a start/stop cycle of getting just enough done to move to the next step.
Multitasking is not doing two or more tasks at once; it's an attempt at rapid task-switching or serial-tasking. I probably don't need to talk much about the likely outcome. It's bad. But how bad is it?
What is the Multitasking Dilemma?
A study by The University of London found that men can experience up to a 15-point drop in effective IQ when multitasking. Women faired better with only a 5-point drop, but both saw a significant decline in their capability and productivity.
A study by The University of Sussex used MRI brain scans to study the effect of habitual multitasking on the brain and found permanent damage and structural changes to the brain. And a series of Hidden Brain podcasts discuss the impact of interruptions on our work life, the benefits of doing less, and the power of deep work.
So, how do we figure out how to balance our increasingly out-of-balance equation of increasing demands versus decreasing resources? Even after we work to eliminate as many interruptions as possible and focus on doing less by actively segmenting and choosing our best customers, we may still find ourselves having to multitask. Is there something from our Lean kit of tools and concepts that might help us?
Think about what multitasking looks like in a manufacturing process. Let's use the following data:
Our production sequence is A, B, A, B, etc. Each batch takes 60 minutes to set up, then 360 minutes to run the 360 pieces. A complete sequence through A and B takes 840 minutes, of which 120 minutes is the time to complete two setups. Our utilization or productivity percentage is (840-120)/840 (all in minutes), which equals 85.7%.
Now imagine that we introduce multitasking, breaking our batches of 360 into batches of 60. We keep switching between A and B every 60 pieces, adding an extra setup every time we change. Our new scenario takes 1200 minutes to complete the same output of 360 A's and 360 B's.
The 720 minutes of production time remains the same, but the 120 minutes of setup time for two setups has expanded to 480 minutes for eight setups. Our productivity drops from 85.7% to 60%. What did all this multitasking accomplish? A couple of the smaller batches of B will get done sooner than before, but the rest of the output will arrive later.
Let us know your thoughts on multitasking by following us on LinkedIn.
Applying Rapid Changeover to the Multitasking Problem
The Lean answer to this multitasking problem is to reduce the 60-minute setup time to gain the flexibility to switch between jobs more quickly, maintaining our productivity levels while gaining flexibility. But can we apply this same Lean methodology to our human processes? Traditionally the rapid changeover methodology, or SMED (Single Minute Exchange of Dies), has been exclusively used in manufacturing, and the focus of the exercise has been the equipment. Can a change in perspective help with our multitasking problem in human work?
Applying the thinking of rapid changeover to our humans allows us to look at the problem from two different angles. The first is very similar to the manufacturing perspective. What are we doing in our work, and can we benefit from the rapid changeover methodology to reduce the damage done by multitasking and improve our capacity? Looking at the four steps of the rapid changeover methodology will help:
- Document the current state. Using whatever tools are needed, observe and document the current processes in place. This process should include physical movement, mental movement (switch applications in the computer, changes of focus, etc.), waiting time, errors made, time to perform tasks versus expected times, etc.
- Move internal steps to external. This is typically the easiest step in manufacturing but might be a little more challenging for a human process. The idea here is to identify actions that could be done before the process begins. For example, a password manager that eliminates the step of looking up passwords or a dashboard that pulls together data from multiple sources to stop the physical and mental movement to gather the data from different locations.
- Streamline remaining internal steps. Can we make the remaining steps in the process easier to perform, and eliminate mental movement where we can?
- Eliminate adjustments. As you document the process, look for places where rework occurs. Whenever someone has to go back and adjust something - the spelling of a name, a hotel room assignment, or the recording of vacation days - that's an opportunity to think about how to error-proof the process and eliminate the time needed to make adjustments. Every piece of rework represents another mental move, forcing us to change our focus to address the rework.
If we can reduce or eliminate the need to "figure out what we're doing" when we change tasks, the impact and loss associated with that change diminishes. We will have eliminated or substantially reduced the setup time, gaining the flexibility needed to respond to an environment where we need to complete lots of different tasks.
The second angle we can take in thinking about setup time and changeovers is to flip our frame of reference completely. What if we introduce a new step in the process, step zero? In step zero, we ask, "What is the productive asset?" By that, I mean, what is the thing that we are stopping to perform the setup on?
Traditionally that's our machines, and now we might think of them as our people. But what if we think of them as our customers?
If we view our processes as our customers experience them, where are we forcing our customers to stop in the process? They may be waiting in line or waiting on us, but their forward progress through the process has stopped either way.
Could we have applied step 2 of the rapid changeover methodology and done something before our customer's arrival to eliminate their wait? Or applied step 3 thinking to streamline the process for the customer? And finally, with step 4 logic (eliminating adjustments), can we eradicate any defects that would result in rework or adjustments for the customer?
Whichever perspective you choose, our constrained labor market is causing us to make hard decisions about how we run our businesses. Lean principles and tools can help us get the most out of our resources. The rapid changeover methodology, previously constrained to be applied only to our machines, provides a simple and new way to examine our human processes to make them less cumbersome for our workers and more productive for our customers.
To read more blogs like this one, and catch up on the latest MoreSteam news, subscribe to our newsletter.
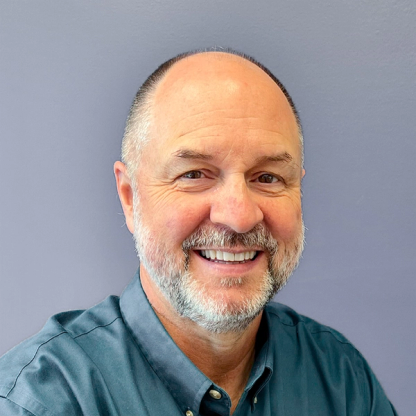
MoreSteam Client Services
Dr. Lars Maaseidvaag continues to expand the breadth and depth of the MoreSteam curriculum by integrating the learning of Lean tools and concepts with advanced process modeling methods. Lars led the development of Process Playground, a Web-based discrete event simulation program. Before coming to MoreSteam in 2009, he was the Curriculum Director for Accenture/George Group and has also worked in operations research and management consulting.
Lars received a PhD in Operations Research from the Illinois Institute of Technology. Prior to his PhD, Lars earned a M.S. in Operations Research and Industrial Engineering as well as an MBA from The University of Texas in Austin.