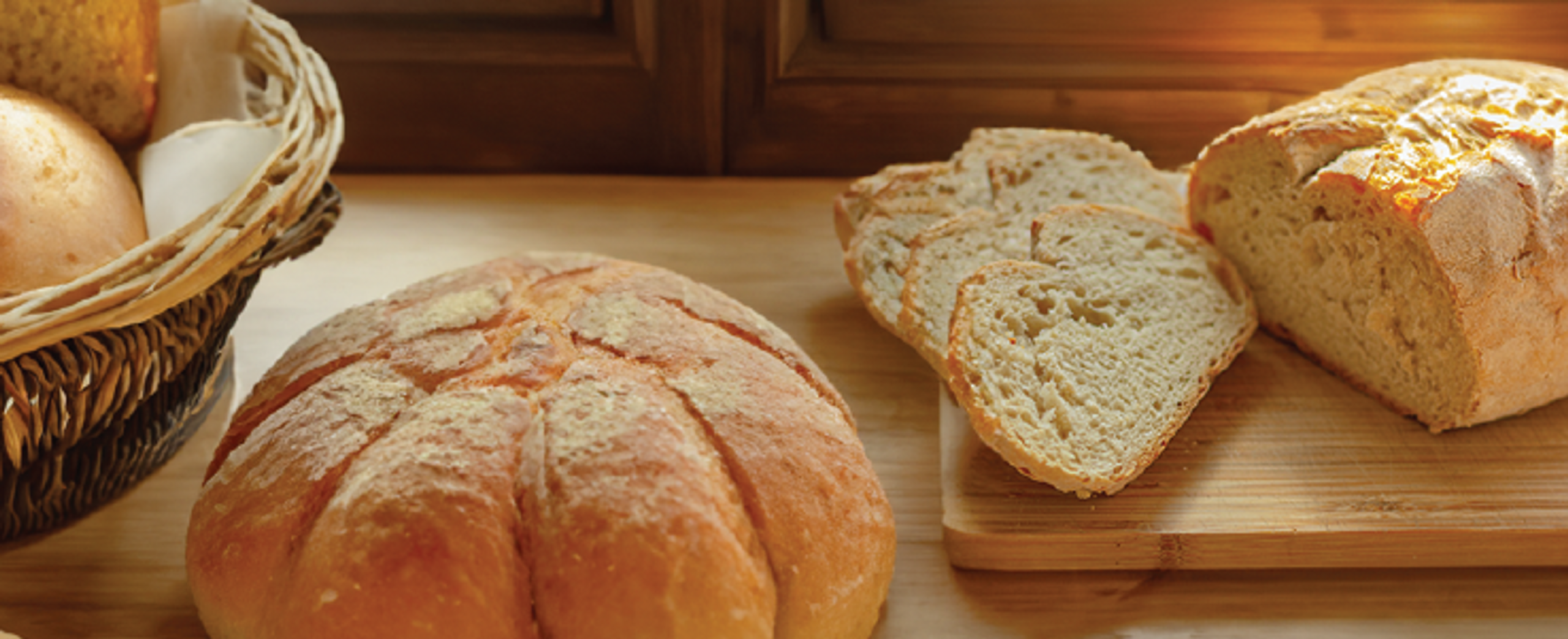
An Introduction to Corrective and Preventive Actions
June 12, 2023Let’s say you want to get into bread-making. You make your first loaf and give it to your best friend, an avid bread-lover. They like it but tell you it’s too dense on the inside; it’s not perfect. You conclude that it didn’t rise enough in the oven. When you look at your bread-making process, you decide you didn’t let it rise enough before baking, so you try again.
Your bread turns out a little better this time, but it's still not where you want it. Nothing like the fresh bread your friend is used to eating.
So, after a bit of research online, you reevaluate your recipe and determine that the loaf would fare better if you used bread flour instead of all-purpose flour.
You go back through your process and keep everything the same, but this time, you switch to bread flour. Success! Your bread rose perfectly, and now you have a baker’s-shop-level quality of bread sitting on your kitchen counter and well-deserved praise from your friendly bread connoisseur. You go back to your original recipe card, scratch out ‘all-purpose flour,’ and write in ‘bread flour’ instead, so you can remember this change in the future.
Little did you know that you just performed a miniature version of a CAPA analysis.
Corrective actions and preventive actions, or CAPA, is a popular quality management approach that organizations use to identify, investigate, and address the root causes of defects, deviations, or failures in their processes, products, or services. It's often triggered by a customer complaint and initiated as a means to avoid any future customer dissatisfaction.
If that sounds like a mouthful, broken down, it’s a measure not unlike Root Cause Analysis that allows organizations to pinpoint mistakes made in their processes, fix them, and take measures to avoid making them in the future.
CAPA is crucial to an organization’s continuous improvement efforts and quality management system. It is common in industries like manufacturing, healthcare, and pharmaceuticals but is valuable to any organization seeking risk mitigation.
Breaking it Down: What is CAPA?
CAPA and Root Cause Analysis are related concepts but serve different purposes. While RCA focuses on identifying the underlying causes of a specific problem or incident, CAPA is a broader process that encompasses RCA and includes the implementation of corrective and preventive actions.
The CAPA acronym involves two moving parts: corrective actions and preventive actions. Despite its name, the “preventive” actions in this process are not always a fundamental piece of the procedure. Organizations only use specific preventive tools when the isolated incident calls for it; this is often in the form of documenting customer complaints or highly sensitive problems. Usually, the corrective actions taken are enough to resolve the problem completely, making it unnecessary to implement standard preventive actions.
Corrective actions address existing non-conformities or failures that have occurred. The focus is on identifying the root cause of the problem and implementing measures to eliminate it moving forward.
Preventive actions are proactive measures taken to identify and mitigate potential issues before they occur, if the analysis calls for it. These actions happen after identifying the root causes of problems, analyzing trends, and implementing corrective actions to prevent reoccurrence.
Also not unlike RCA, some common Lean Six Sigma tools and methods to use while performing CAPA include:
- Fishbone Diagram
- 5 Whys
- Process Mapping
- Failure Mode and Effects Analysis (FMEA)
- Pareto Analysis
- Control Charts
- DMAIC
Explore our OpEx Insights Page for More Blogs Like This One!
A Step-by-Step Overview of the CAPA Process
The specifics of the CAPA process may vary depending on the organization, industry, and specific needs. But here’s a general framework for implementing CAPA:
Initiating and Planning
- Identify the Issue: The more specific you are in this step, the more successful the outcome of the analysis. The issue could spawn from a customer complaint, defective products, or a deviation from standard procedure.
- Initiate CAPA: Document the problem and create a CAPA record or form. This record will be the source of all information related to the CAPA process, making it a crucial element in the procedure.
- Form a CAPA Team: Assemble a cross-functional team from relevant departments that include individuals with expertise and knowledge specifically related to the issue.
- Investigate the Issue: Conduct a thorough investigation to determine the root cause(s) of the problem. This step involves collecting data, examining relevant records, analyzing trends, and utilizing problem-solving techniques like 5 Whys and fishbone diagrams.
Executing and Correcting
- Identify Corrective Actions: Based on the investigation findings, determine corrective actions that address the issue’s root cause(s). The focus is on eliminating the immediate problem and preventing its recurrence.
- Develop an Action Plan: Create a detailed plan outlining the steps required to implement the corrective actions. Assign responsibilities, set deadlines, and define milestones to ensure proper execution.
- Implement Corrective Actions: This step might look like process changes, equipment repairs, training programs, or policy updates, depending on the investigation results.
- Monitor and Verify: This step is imperative to ensure that the actions taken produce the desired results and resolve the problem. Examples of continuously monitoring the effectiveness of the actions include follow-up inspections, testing, audits, or other verification methods.
- Document and Communicate: Thoroughly document all actions taken throughout the CAPA process, including the investigation findings, corrective actions, implementation details, and verification results, and communicate this information to relevant stakeholders.
- Preventive Actions: As part of the CAPA process, you may also need to consider implementing preventive actions to minimize the likelihood of similar issues occurring in the future. These proactive measures include risk assessments, process improvements, training programs, or enhanced quality controls.
Wrapping Up
- Review and Close CAPA: Periodically review the CAPA process to assess its effectiveness and make necessary improvements. Once the corrective actions have been successfully implemented and verified and preventive measures are in place, close the CAPA by documenting the closure and archiving the CAPA record.
For More In-Depth Articles on Lean Tools and Methods, Check Out our Toolbox Page!
Best Practices for CAPA Success
It’s essential to understand some best practices that contribute to a CAPA’s effectiveness and success:
- Clear Policy and Procedures: Establish a clear CAPA policy and define detailed procedures that outline the roles, responsibilities, and steps involved in the process. Ensure that employees understand the policy and have access to the necessary documentation and training.
- Leadership Commitment: Obtain commitment and support from top-level management to prioritize CAPA implementation. Leaders should actively participate in the process, allocate resources, and communicate the importance of CAPA throughout the organization.
- Root Cause Analysis: Emphasize the importance of thorough root cause analysis. Use appropriate problem-solving tools and techniques to identify the underlying causes of issues and avoid treating symptoms rather than addressing the true root causes.
- Data-Driven Decision Making: Base CAPA actions on objective data and evidence. Collect and analyze relevant data to drive decision-making, monitor trends, and identify recurring issues that require corrective or preventive actions.
- Cross-Functional Collaboration: Foster collaboration and communication among departments and teams involved in the CAPA process. Encourage cross-functional participation to leverage diverse expertise and insights, enabling a comprehensive understanding of the issues and effective problem-solving.
- Timeliness and Proactivity: Address issues on time. Promptly initiate CAPA when problems arise to prevent escalation and minimize potential impacts. Additionally, emphasize proactive preventive actions to anticipate and mitigate potential issues before they occur.
The Bottom Line
CAPA is a vital process for many reasons. Not only does it help your organization keep a pulse on the ongoing issues within your workspace, but it’s also a great way to leverage data for future continuous improvement initiatives.
Corrective actions aim to fix the immediate issue and prevent it from happening again, while Preventive actions focus on stopping problems from happening in the first place. Working in tandem with one another creates an iterative, continuous improvement process imperative to an organization’s quality management system.
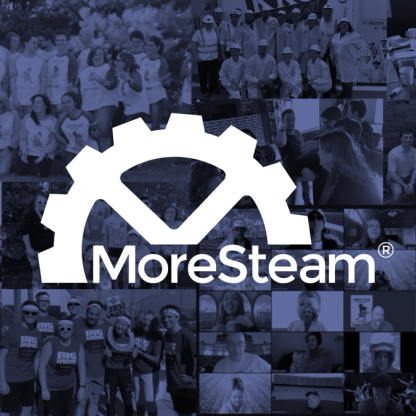
MoreSteam's Enterprise Process Improvement platform includes the tools, training, and software you need to transform your organization, large or small, into a problem-solving powerhouse. Our products are trusted by over half of the Fortune 500 and by other organizations and universities worldwide. When you partner with MoreSteam you gain a team dedicated to helping you succeed.