
Exploring the Evolution of Continuous Improvement
From Germany to America and back, Arnd Huchzermeier has always had a finger on the pulse of continuous improvement.
For the past 28 years he's been a Chaired Professor of Production Management at the WHU — Otto Beisheim School of Management in Germany, which is widely recognized as the #1 business school in the country. WHU is also a partner of the prestigious Kellogg network, featuring top business schools around the world.
In addition to his role as a professor, Huchzermeier is the Co‐Founder of the INSEAD‐WHU Industrial Excellence Award, benchmarking management quality for competitiveness in the industrial and service sectors. It is the most prestigious industry competition in Europe, and Huchzermeier helps select each year's champion.
Before returning to his home country of Germany in 1993, Huchzermeier spent several years in the United States - first as an employee for Siemens Corporate Research in Princeton, and later as a professor at the University of Chicago's Booth School of Business. With decades of industry experience under his belt, Huchzermeier has a wealth of knowledge about the evolution of Lean Six Sigma and the impact it will have on the next generation of business leaders.
We asked him to share some thoughts about where we've been and where we're going next.
Through your role with the Industrial Excellence Award, you get a close look at what other companies do every year to be successful. What are some of the most common traits you see among the award‐winning organizations?
The most common thing is high growth rates. Their financials are very positive – far above average profitability. The most successful ones grow over 100% from year-to-year. The way they achieve that is through end‐to‐end visibility. They have a clear focus on interacting daily with their teams, making sure everyone understands their role, and using market feedback for constant product and process innovation.
BMW is the benchmark on strategy deployment here in Germany. Members of the management team meet with their teams every morning to ask the same few questions: "What have you done since yesterday? What are you going to work on today? What problems are you facing? How can we help you overcome those problems?" Everyone in the organization – at every level – truly understands the company strategy and how they contribute to it.
Many German companies are run by former BMW employees these days, because they were so successful in laying the groundwork for this.
What's the biggest difference you've seen between continuous improvement efforts in the U.S. compared to Europe?
U.S. companies are very, very fast. They make radical changes, and when they do something, they support it with mass training. They make an enormous investment to train thousands of people in one shot. So, they go faster, and they're also willing to take more risk with new technologies.
In Europe it's all about continuous improvement. They're diligent about making progress, but speed isn't as much of a priority. Both have their advantages. Digitalization is another big topic everywhere. Americans especially are more focused on platforms and the user interface.
During your three decades as a professor in production management, how has the subject material evolved?
In the early days it was all about resource optimization. People solved mathematical equations for optimizing process utilization or output. Today everything is driven by machine learning. There's more information to drive your prediction of customer demand, which is key because that impacts all other operational decisions in the supply chain, e.g., inventories and capacities.
What you need in the future is more trust‐building. You need to trust the information up‐stream. Is the inventory there? Will it be ready when it's needed?
The impact of artificial intelligence is also significant. You look at automotive, the process is fully automated by robots now. There's also more data to analyze. As more industries begin relying on AI for continuous improvement, the potential is there for them to break through and jump to the next level.
Are there any elements that you feel are often overlooked - either by companies or other universities teaching the course material?
Fairness is often overlooked. What does that mean? Fairness is about giving everyone regular opportunities to communicate and contribute, mostly from the frontline to the top. We teach this as a process. Whenever you're making a decision as an organization, ask all the people involved to come together and work through five "E's":
- Engage — Bring together everyone impacted by the decision
- Explore — Look at all the options as a group
- Explain — Make sure everyone understands why the decision was made
- Execute — Start doing the work
- Evaluate — Correct the group's decision if the desired result is not realized
Then there's also usually a post‐evaluation process as well, to judge how effectively everything went.
How do you use MoreSteam's eLearning and simulations to help prepare your students for the business world?
MoreSteam is a fantastic training tool for our students in all programs, including Bachelors, Masters and MBAs. They like it a lot – it works really well with our German base. We have a lot of students whose parents work in or run companies where this training is relevant, and word is getting out. They're starting to create more process understanding in their own companies.
You recently ran the Inbox simulation with your students for the first time, helping them understand how Lean concepts apply to transactional processes. How was that experience?
They really enjoyed it. At first they thought it would be a boring process, but they quickly saw how engaging it can be. They liked working in teams — we had two competing teams, and everyone had to optimize their own role within the process. It was a unique way to push the students and help them learn something new through application.
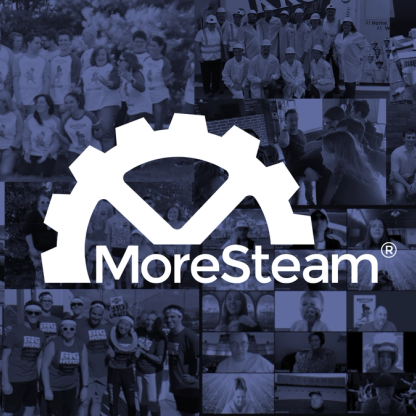
MoreSteam's Enterprise Process Improvement platform includes the tools, training, and software you need to transform your organization, large or small, into a problem-solving powerhouse. Our products are trusted by over half of the Fortune 500 and by other organizations and universities worldwide. When you partner with MoreSteam you gain a team dedicated to helping you succeed.