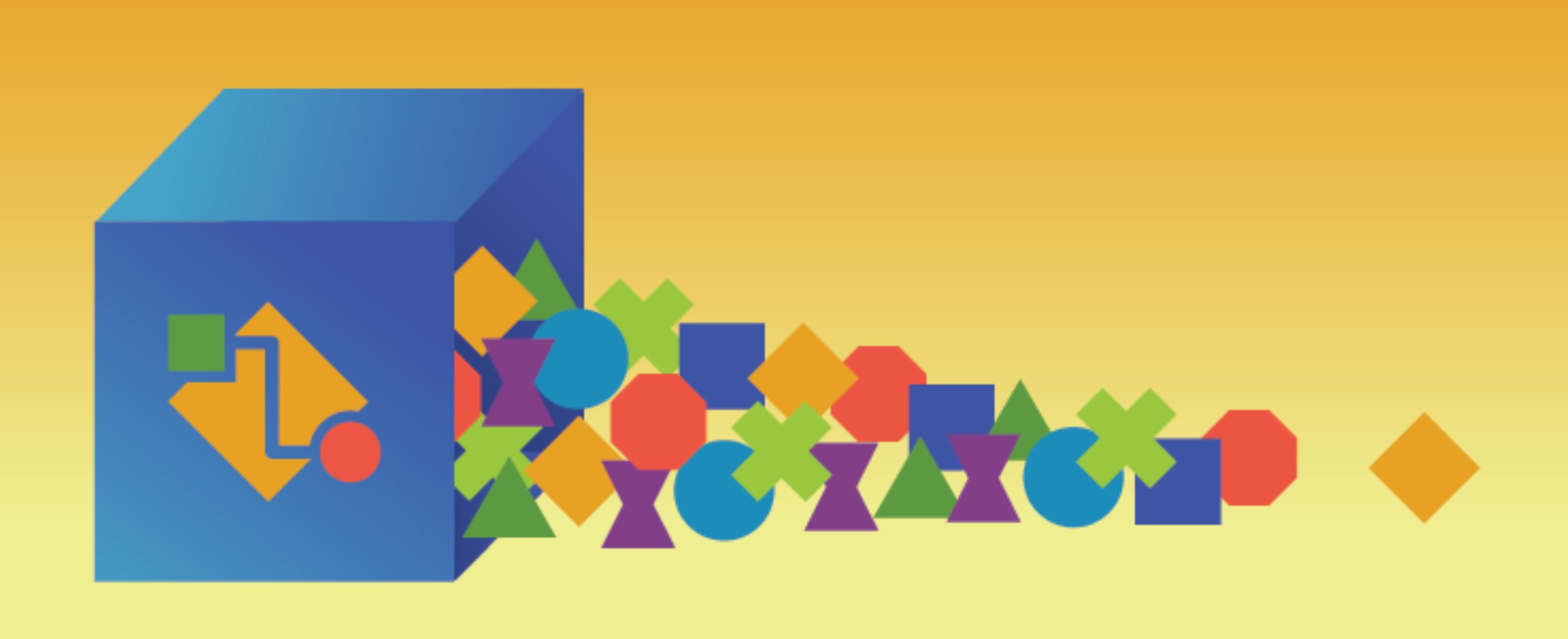
Reflections on How Far Process Modeling Has Come
March 21, 2023As we approach the 15th anniversary of the introduction of Process Playground (and the 10th anniversary of EngineRoom), I have been reflecting on the evolution of continuous improvement work and processes in our organizations.
When we first introduced discrete event simulation with Process Playground, we thought of it along the lines of Design of Experiments: a tool that could be used occasionally, in very specific circumstances, for a fairly narrow range of problems.
As the years have moved on, it has become increasingly clear that process modeling is no longer an optional or occasional effort. The need to rapidly adapt and change processes is the new norm for our organizations.
Collecting data over a long period from a stable process has become increasingly challenging as the parts move too fast. The increasing complexity of product and service offerings, rapid swings in demand patterns, faltering supply chains, and a pandemic have shown that we need to adapt quickly and have very little time to perfect our processes.
Failing to Prepare is Preparing to Fail
Several clients now have process modeling with Process Playground as a critical, required step of nearly all continuous improvement work. The models expand the boundaries of possible improvements, allowing the opportunity to study and adopt process improvements well outside the traditional scope of small, incremental ones.
The models are also used to predict how the process will perform when confronted with various failure modes, such as staff and material shortages or demand mix changes, and how to react and adapt to those changes. Think of it as FMEA+, where the plus part creates a checklist of corrective action responses to the failure modes tested in the process model.
With the move from specialist to standard work, process modeling has entered the toolkit of all continuous improvement practitioners. Flattening the learning curve and lowering the cost of modeling has always been a primary goal for Process Playground.
Whether for use in a Lean Six Sigma project or to support training by creating 'virtual Gemba' process models for the students to work with, process modeling has become an integral part of the continuous improvement world.
The following blog was first published twelve years ago as we ramped up Process Playground's use.
The introduction is perhaps a little much (and doesn't really sound like me, so I'm attributing it to our marketing department). However, once you get past the Shakespeare reference, the message is still pertinent today. It provides a good guide on when to use simulation as part of your continuous improvement project. We've found with several of our clients that the answer to the question is, 'almost always.' Just like process mapping.
To model, or not to model, that is the question: Whether 'tis nobler to model or to suffer The slings and arrows of a failed live pilot…
The decision to create a simulation model of an improvement solution is a tough question. Not quite as tough as Shakespeare's soliloquy on the existential nature of life, but a tough decision all the same. There are many trade‐offs to consider, and the answers are not always clear.
Step One: Evaluate Your Variations
A simulation model aims to provide greater insight into a proposed solution. An insight that you can't gain through other methods.
So, the first question to ask is:
(1) "Is my proposed new process sufficiently complex that traditional LSS tools cannot adequately predict the performance and interactions that may occur?"
Typical indicators that the answer to this question might be "yes" may include:
Task Variation — My process has to respond to a high degree of variation in the types of products or services it handles. High task variation in a process can often lead to unanticipated queues and shifting bottlenecks. A simulation model can help identify the process's potential range of queue lengths and utilization levels for the process.
Demand Variation — High variation in demand can also lead to unintended effects. A traditional approach to 'sizing' the capability of a process with high variation in demand is to perform steady‐state calculations at the low‐volume and high-volume states. The results of those calculations then help us determine staffing levels, inventory levels, etc., for the process.
However, the steady‐state calculations don't give us any information about the transitions between high and low demand points. How early should we add staff? How long should we retain staff after the high demand 'rush' has passed? Simulation modeling can help determine the performance of the process during these dynamic periods.
Process Variation — Think about a finance department as a job shop where we have several similar (but not equal) resources and jobs (month‐end close, capital investment, cash flow management, etc.) flowing through the department.
Just as in a manufacturing job shop, it is difficult to anticipate how a process will perform if the work flowing through the process can take many alternative paths. Bottlenecks constantly move, and queues can spontaneously form where you least expect them.
Complex processes like this can benefit tremendously from a simulation model to help define the initial process and 'stress test' the process in the future when considering new or special projects. The simulation model can help determine if the process can handle the changes.
Step Two: Crunch the Numbers
The next question to ask is:
(2) What is the cost comparison between running one (or more) 'Live' pilots versus building the simulation pilot?
The following table compares some of the risks and benefits of Live versus simulated pilots:
Step Three: Make the Decision
So, the final question:
(3) Do I build a simulation or not?
Maybe. Simulation is underused in today's LSS world, and part of that is due to the high investment required to learn most of the simulation software on the market. MoreSteam created Process Playground to help address this gap. Process Playground is easy to use and easy to learn. Our software takes the 90/10 approach — we can do 90% of the models you may need to build with 10% of the effort. After you have become a pro at building models with Process Playground, you can move on to a larger simulation package when your models need to jump up to a high level of complexity.
Simulation can be a powerful addition to your toolkit for process improvement and open up new, out‐of‐the‐box thinking about your processes. But it must be tempered by careful cost/benefit analysis to ensure that the building of simulation models remains a means‐to‐an‐end and not an end in itself.
—Dr. Lars Maaseidvaag
Editor's Note: This post was originally published on December 20, 2011, and has been updated for accuracy and comprehensiveness.
To Stay Up-to-Date on All Things Process Improvement, Subscribe to Our Newsletter!
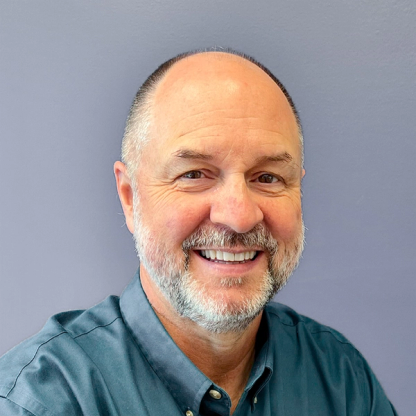
MoreSteam Client Services
Dr. Lars Maaseidvaag continues to expand the breadth and depth of the MoreSteam curriculum by integrating the learning of Lean tools and concepts with advanced process modeling methods. Lars led the development of Process Playground, a Web-based discrete event simulation program. Before coming to MoreSteam in 2009, he was the Curriculum Director for Accenture/George Group and has also worked in operations research and management consulting.
Lars received a PhD in Operations Research from the Illinois Institute of Technology. Prior to his PhD, Lars earned a M.S. in Operations Research and Industrial Engineering as well as an MBA from The University of Texas in Austin.