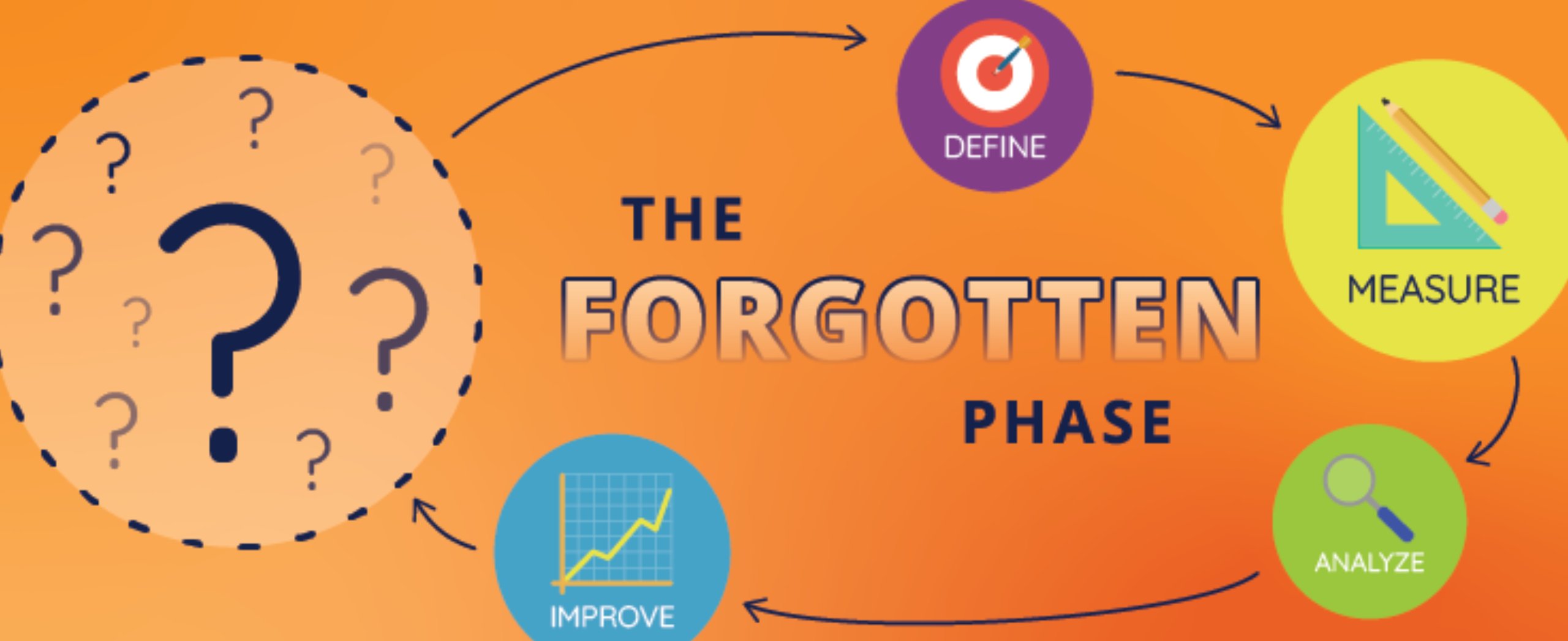
Why the Most Critical Phase is Often the Most Overlooked
May 31, 2022When looking at process improvement projects, many of them resemble running a fast break in basketball. The ball is rebounded. The outlet pass is made. The ball advances up the floor, with lanes filled by players hustling down the court. Everything is running smoothly until…the lay-up is missed.
The control phase is like "finishing" the fast break after all the other pieces are accurately put into place. Though the shot may look simple, and may even be one of the first skills you learn as a basketball player, it definitely can not be taken for granted. Several missed lay-ups can make or break your entire game.
The control phase in a DMAIC project is arguably the most important, yet it is often the most overlooked. This is because the control phase often relies on human behavior to change in order to be effective.
The control phase is imperative because it's a result of the hard work from the first four phases (define, measure, analyze, improve).
The control phase is seen (and underutilized) so often in our everyday lives.
Utilize the 5 C's (communicate, confirm, convenience, compel, and check) in the control phase to execute effectively.
Controlling our Personal Hygiene
According to the CDC, on average, healthcare providers are washing their hands less than half of the times they should be. The Center for Disease Control has been campaigning for more frequent hand washing in the healthcare industry well before the Covid-19 pandemic. This ongoing issue, which has a seemingly simple solution (just wash your hands), is harder to implement than you'd expect. And that's because of human interference.
Like any effort to influence human behavior, merely issuing instructions is not sufficient. Institutionalizing the improvement requires compliance, and real compliance requires more than an updated policy manual. In spite of the CDC's efforts to share best practices and guidelines designed to stop the spread of infection from contaminated hands, compliance rates remain dismal.
Not a very reassuring statistic, is it? However, hospitals that employ active monitoring, positive reinforcement, punitive measures for repeat offenders, and collaborative design of the process and facilities will experience much higher compliance rates. Why? These hospitals have taken the time to utilize tools in the control phase.
Here's a framework for thinking about the control phase that might be useful — 5 attributes of a good control strategy based on 5‐C's:
Thinking Critically About the DMAIC Control Phase
Utilizing these 5C's as part of your control phase will help your organization achieve a higher compliance rate for implemented improvements. Or help you with your lay-ups, whichever you prefer.
1) Communicate — The process must be clearly and actively communicated and should explain why the process is essential. Communicating the why establishes the connection between cause and effect and broadens organizational process knowledge. The best communication is pushed through multiple channels using different visible forms of media (audio, video, text messages, signage at point of use). Changing written procedures in a binder that nobody ever looks at does not change process behavior.
2) Confirm — An assessment and check‐off should actively confirm understanding of the requirements. This procedure eliminates future excuses like: "I didn't understand the requirements."
3) Convenience — The more convenient the process is, the more likely your employees will follow it. Placing a hand‐washing station down the hall and up a flight of stairs won't yield much use. Returning to the WSJ article: "according to Charles Huskins, an author of the IHI toolkit for hand hygiene and an infectious‐disease expert at the Mayo Clinic in Rochester, MN, compliance rates at Mayo hospitals were sharply improved, in part, because employees were allowed to test different alcohol hand rubs, and chose one with strong moisturizers to avoid irritation that might lead to discontinued use." Involving the process operators in the process design almost always improves the result.
4) Compel — Positive and negative incentives are necessary to both "pull" and "push" employees toward compliance. A compliance program with no teeth is no program at all, just wishful thinking.
5) Check — Results must be monitored and measured to gauge success or failure and provide feedback on the first four "C's" effectiveness.
That's my 2 cents,
Bill Hathaway
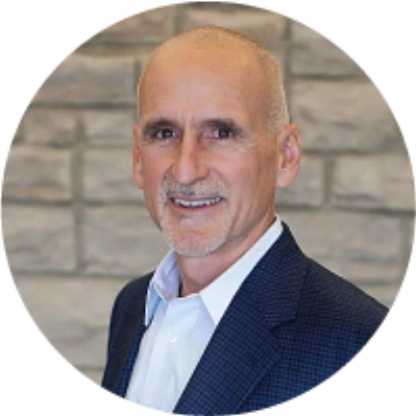
CEO • MoreSteam
MoreSteam is the brainchild of Bill Hathaway. Prior to founding MoreSteam in 2000, Bill spent 13 years in manufacturing, quality and operations management. After 10 years at Ford Motor Co., Hathaway then held executive level operations positions with Raytheon at Amana Home Appliances, and with Mansfield Plumbing Products.
Bill earned an undergraduate finance degree from the University of Notre Dame and graduate degree in business finance and operations from Northwestern University's Kellogg Graduate School of Management.