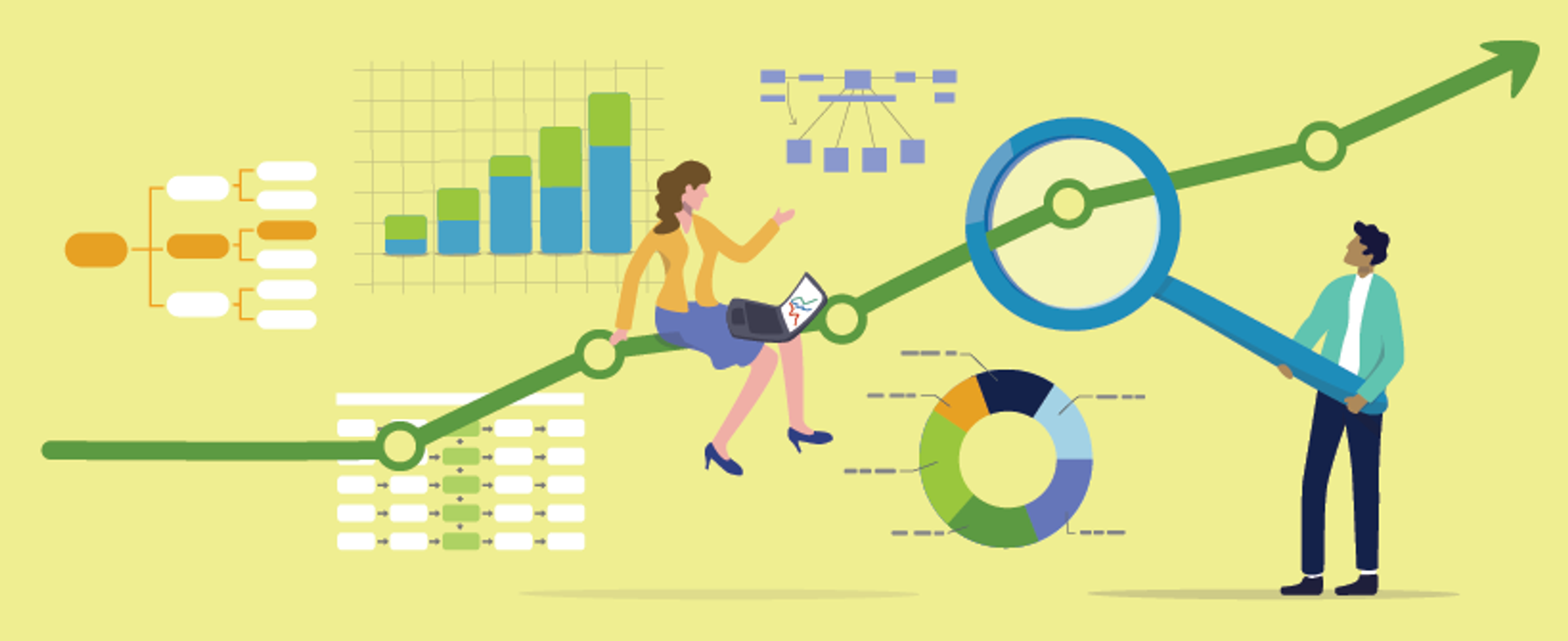
A Beginner's Guide: What is Lean Six Sigma?
August 30, 2023If you’re new to the world of continuous improvement and don’t know the first thing about Lean Six Sigma, your mind might be flooded with questions:
- What are the core elements of Lean Six Sigma?
- What are the belt levels, and which certification is right for me?
- How robust are the certification programs?
- Do I need prior knowledge in continuous improvement?
There’s a lot to learn in this industry, and figuring out where to start can be overwhelming. If you’ve begun your research, you know that earning a belt-level certification in Lean Six Sigma is highly advantageous to your career. It is a huge step in becoming a process improvement expert. A certification at any level will help you gain confidence in your role by becoming an asset to your organization and helping improve the bottom line.
But the internet is flooded with information about Lean Six Sigma and what each certification program entails. An abundance of information can make determining what to expect with your training, courses, and projects challenging.
And while it’s not untrue that there’s a lot to learn, knowing and understanding the core elements of Lean Six Sigma is all you need to feel comfortable starting your certification journey.
What is Lean Six Sigma?
Understanding the basics is essential before determining which belt-level training or certification is right for you. At its core, Lean Six Sigma is a team-focused approach that seeks to improve performance by eliminating waste and defects.
It’s a comprehensive methodology that combines two powerful techniques—Lean and Six Sigma— and, when implemented together, provides a cohesive process-improvement strategy.
- Lean is the philosophy that any component of the company that isn’t directly benefiting the bottom line is unnecessary. Lean principles focus on eliminating waste and optimizing process flow to maximize customer value.
- Six Sigma is a data-driven methodology aimed at reducing defects, variability, and errors in processes. It focuses on achieving high levels of quality by using statistical analysis and problem-solving techniques.
Some fundamental principles of Lean are:
- Value: Identifying the value the customer perceives and focusing on activities that directly contribute to that value.
- Value Stream: Mapping and analyzing the end-to-end processes to identify waste, bottlenecks, and non-value-added activities.
- Flow: Ensuring smooth and uninterrupted workflow by minimizing interruptions, delays, and batch processing.
- Pull: Establishing a customer-driven workflow where products or services are pulled based on actual demand.
- Continuous Improvement: Encouraging a culture of ongoing improvement through eliminating waste and pursuing perfection.
The core elements of Six Sigma include:
- Data-Driven Decision Making: Six Sigma heavily relies on data analysis to make informed decisions. The data collected during the Measure and Analyze phases are used to identify patterns, trends, and root causes of problems.
- Reducing Process Variation: Six Sigma aims to minimize process variation and maintain consistent performance. By reducing variation, the process becomes more stable and predictable, leading to better quality outcomes.
- Focus on Customer Requirements: Understanding and meeting customer needs is a fundamental aspect of Six Sigma. Lean Six sigma emphasizes the importance of delivering products and services that align with customer expectations.
So, let's put this together. When combined, Lean Six Sigma focuses on:
Value to the Customer: Lean Six Sigma strongly emphasizes understanding and meeting customer needs. It involves gathering customer feedback, identifying critical-to-quality requirements, and aligning improvement efforts to deliver customer value.
Improving Business Processes: Lean Six Sigma employs various tools and techniques to identify and eliminate waste, streamline workflows, and optimize process flow.
Making Decisions with Data: A key aspect is using data and statistical analysis to make decisions.
Reducing Process Variation: Six Sigma reduces process variation and defects by applying statistical analysis and control techniques.
Removing Waste: Lean focuses on identifying and eliminating the ‘8 Wastes,’ which include overproduction, waiting time, excess inventory, unnecessary motion, defects, and more. This can be a lot of different processes in a lot of different industries. Lean Six Sigma has been used to improve wait times in an emergency department, decrease the scrap rate in a toilet manufacturing process, redesign the makeline at a pizza restaurant, and improve the time to receive a permit from the department of buildings in a fast-growing city.
The Lean Six Sigma Approach
Lean Six Sigma is a structured approach to problem-solving driven by asking appropriate critical questions in the right order to lead to a solution. One of the more common roadmaps in Lean Six Sigma problem-solving is the DMAIC method. The DMAIC method breaks down problem-solving into manageable phases, ensuring a methodical journey toward implementing sustainable improvements.
The phases of DMAIC are:
- Define: Clearly defining the problem, the project goals, and the customer requirements.
- Measure: Collecting data and analyzing process performance to understand the current state and identify key metrics.
- Analyze: Applying statistical analysis to identify the root causes of defects or variations in the process.
- Improve: Implementing solutions to address the identified root causes and improve the process performance.
- Control: Establishing controls and monitoring systems to sustain the improvements and prevent regression.
Within each phase several Lean Six Sigma tools and techniques are utilized. Some examples include:
- Value Stream Mapping
- Process Mapping
- Root Cause Analysis
- CTQC Tree Diagrams
- Statistical Process Control
- Kaizen Events
- Fishbone Diagrams
- Measurement System Analysis
This is by no means an exhaustive list, and as you develop your skills in process improvement, all of these tools and techniques will become second nature to you.
For a More In-Depth Explanation of DMAIC, Check Out Our Blog: What is the DMAIC Methodology?
What makes Lean Six Sigma a success?
When used together, Lean Six Sigma offers a structured approach to solving problems in an organization. But it's not successful by itself. For sustained improvements in an organization, problem-solving needs to become part of a larger cultural change in an organization. Everyone must participate.
Teamwork and Collaboration: Cross-functional teamwork and collaboration are essential in driving improvement efforts. Process efficiency involves engaging stakeholders, building a culture of continuous improvement, and fostering collaboration between different departments.
Leadership Engagement: Leadership support and engagement are crucial for implementing Lean Six Sigma. Leaders provide direction, allocate resources, and encourage a culture that drives data-driven decision-making.
Which Lean Six Sigma Certifications Can I Earn?
It’s crucial to understand that Lean Six Sigma certification has no authoritative voice. Different programs and organizations offer various measures of volume, practice, and rigor. But generally speaking, the belt-level titles you can earn are White, Yellow, Green, Black, and Master Black.
As you advance in belt level, you sharpen leadership skills and build technical capability. Each belt level, regardless of color, allows you to bring more value to your workplace, and the more you advance, the more rigorous certification becomes.
But not everyone needs to be a Master Black Belt. Landing on the proper training for you depends on the problems you need to solve and where you see your career path going.
What are the Belt Levels I Can Earn?
When it comes to Lean Six Sigma, there are a few different belt levels that one can achieve:
- White – The White Belt level of Six Sigma training offers a basic understanding and awareness of problem‐solving principles.
- Yellow – Yellow Belt holders have a basic understanding and overview of Lean Six Sigma concepts and tools. Once trained, Yellow Belts can expect to participate as a team member on a project, typically led by a Green Belt.
- Green – Green Belt certification goes more in-depth than a Yellow Belt with Lean Six Sigma concepts and is a very popular option for those looking to become project leaders.
- Black – Black Belt training takes significantly more time and effort than Yellow or Green Belt training but is perfect for those seeking leadership roles in project management or process improvement. Since this level requires a substantial amount of training, Black Belts can expect to run more advanced projects requiring heavy stats or Designed Experiments.
- Master Black – The Master Black Belt certification, or the highest level of certification in Lean Six Sigma, will help you become an expert in operational excellence. A rare belt‐level achievement, Master Black Belts are seasoned Black Belts that will have extensive advanced training in design, stats, and modeling.
To Learn More About Belt Certifications, Check Out Our Blog: Lean Six Sigma Belt Levels Explained
The Bottom Line
As an individual, earning a belt certification at any level automatically increases your chances of:
- Achieving a higher wage in your current position
- Grabbing the attention of prospective employers with an impressive resume
- Leveraging for a higher position or promotion within your organization
Whether you are seeking certification on your own or you’re an organizational leader looking for ways to increase process efficiency, having even a baseline understanding of Lean Six Sigma is advantageous to your business’s bottom line.
Certification provides valuable skills, knowledge, and credentials that can boost employee career prospects and increase the efficiency of process improvement initiatives for organizations.

Erin Valusek
Content Writer
MoreSteam